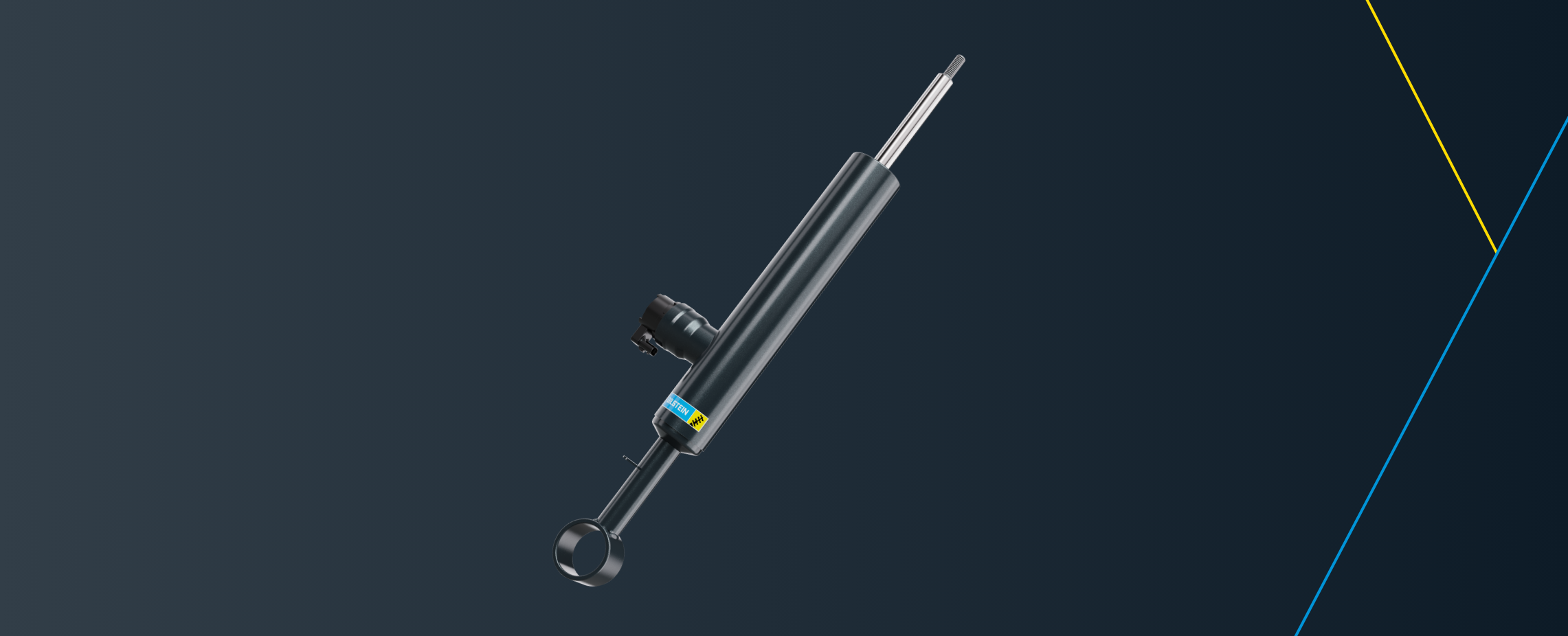
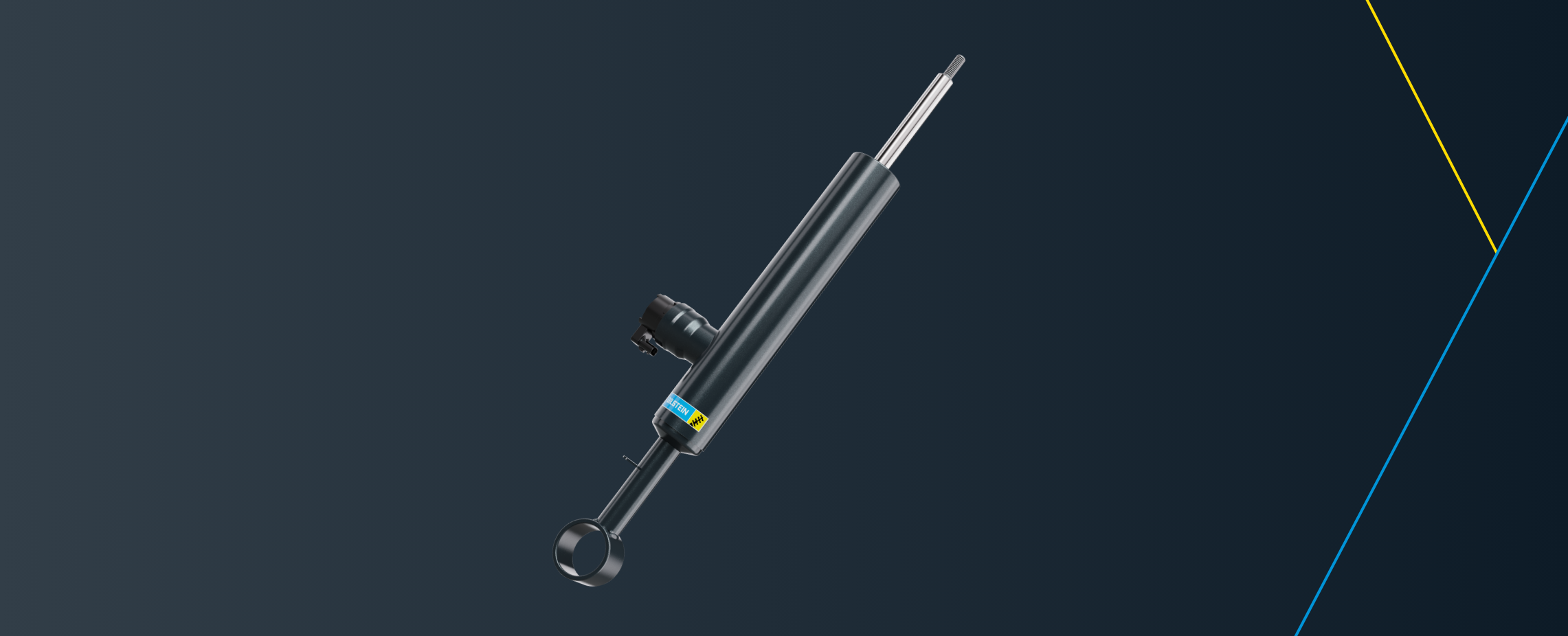
BILSTEIN DampTronic® II: Redesigned for mass production
With DampTronic® II, BILSTEIN has a semi-active chassis technology in its range that enables an enormous spread between sporty and particularly comfortable driving behaviour, especially in original equipment. This article explains what the system can do and how the developers were able to transfer the technology from small to large-scale production for a premium car manufacturer.
After BILSTEIN’s Aftermarket department launched the technology originally developed by the OE division in 2017, Jürgen Schneider took over responsibility for BILSTEIN DampTronic® II in the original equipment sector at the end of 2017. For the demanding requirements of a leading car manufacturer, the semi-active chassis system seemed to represent the perfect balancing act between high technical demands and a healthy awareness of costs.
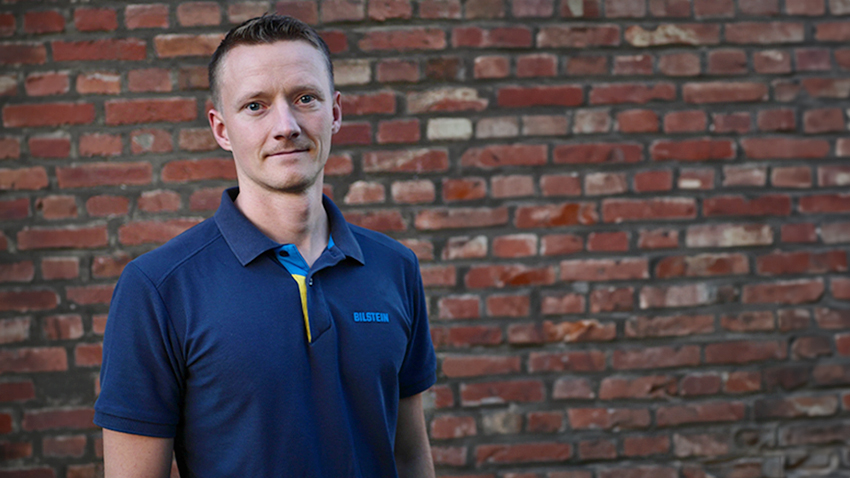
BILSTEIN DampTronic® II resolves the conflicting goals of sportiness and comfort
At the time, BMW wanted a chassis solution that offered a high spread between sportiness and the greatest possible comfort. Designed as an infinitely variable damper, BILSTEIN DampTronic® II enables the compromise between ride comfort and driving dynamics to be resolved even further for a wide range of driving situations.
Jürgen Schneider “We have classic spring disc valves for the hard damping characteristics in the rebound and compression stages, as well as for the soft damping characteristics. In between these, an adjustment valve works, which precisely approaches each individual force point in the operating area by changing the current intensity between soft and hard detection. The damper works using the UniFlow principle, whereby the oil flows through the valve in the same direction in both the rebound and compression stages.”
Semi-active chassis technology
“The important thing is that all three passive valves and the adjustment valve must be perfectly harmonised with each other to achieve the desired function of the damper,” the engineer explains. “We can customise the characteristic curves according to the customer and vehicle requirements profile. Between these two, we have our adjustment valve, where we can adjust the intermediate characteristics depending on the electrical currents between 0 and 1.8 amps.” This not only opens up countless possibilities for tuning the characteristic curve – and therefore the characteristics of the chassis. Jürgen Schneider: “Passive valves usually work more dynamically than semi-active valves and are very stable, which massively increases the reproducibility of the damping forces. And our directional control valve works between the two, which is more comfort-orientated compared to competitor systems.”
We love setting benchmarks. With our innovative technologies, we are shaping the present and the future of damper design. Find out all about the most exciting BILSTEIN technologies here.
Read moreFrom small to large-scale production
The system therefore has decisive advantages over other technologies. But there were two significant hurdles. “The original system established in the aftermarket was only designed for small series and also required cost optimisation in order to meet the requirements of OE customers from the original equipment sector,” says Jürgen Schneider. The BILSTEIN DampTronic® II technology therefore had to be transferred to large-scale production, which at BILSTEIN is characterised by a high degree of automation.
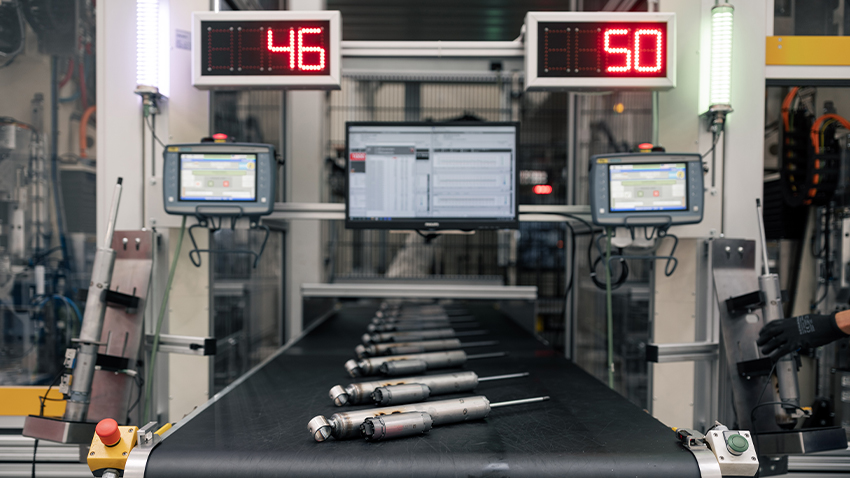
Advanced Development Process
The newly introduced “Advanced Development Process” (ADP) at BILSTEIN played a key role here. The basic function was developed in this process before the technology was handed over to the customer project as part of a transition phase.
The ADP process is designed as a structured, methodical approach with which innovative technologies and products are systematically developed and tested on the basis of overarching targets – such as time or cost targets – in order to ensure their market readiness before they go into series production.
Jürgen Schneider “The process goes through various development stages, which we refer to as gates. The DampTronic® II project started with a redesign as the first gate. Certain details and components were revised or replaced so that they could be produced profitably in large quantities.”
As part of the “Design Verification Plan” (DVP), the BILSTEIN test engineers subjected the revised concept to an extensive testing programme. The BILSTEIN DampTronic® II shock absorbers underwent extensive testing in the defined procedure – from test bench tests and simulations to the legendary BILSTEIN road test, both internally at BILSTEIN and together with the customer.
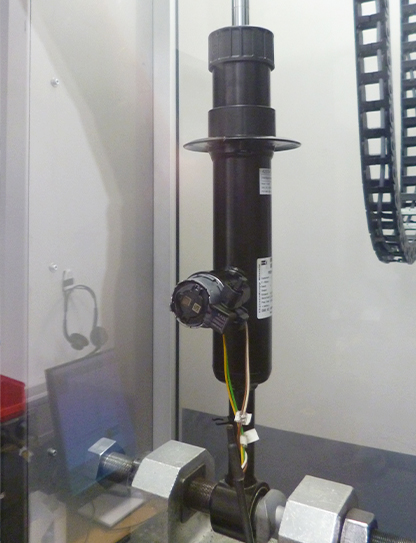
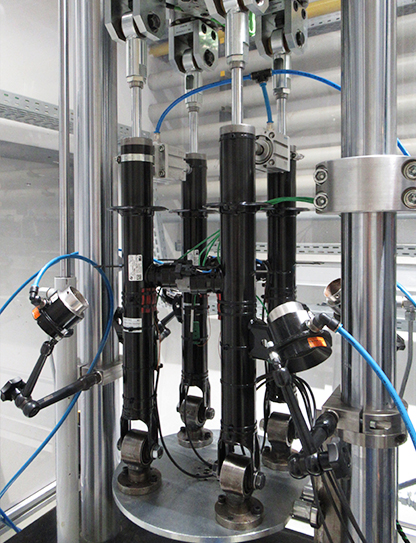
Teamwork at BILSTEIN
While the system was already impressive in terms of driving dynamics, Jürgen Schneider and his team from BILSTEIN Advanced Engineering had to face another challenge. “At that time, we had established spray painting on all systems at BILSTEIN. However, a clear customer requirement was a paint finish using the cathodic dip coating process,” recalls Jürgen Schneider. The cathodic dip coating is characterised by very strong corrosion resistance.
Jürgen Schneider “For us, this meant that we also had to take this type of aftercare into account in the design. Here, we benefited from our close interdepartmental dialogue at BILSTEIN to jointly develop the perfect solution for the customer.”
Jürgen Schneider is convinced that teamwork was also a key to success in this project. “Such large projects can only be managed by a well-functioning team. This meant that we were not only able to count on strong support from our testing department, which put the damper through its paces. Working together with the purchasing department, new suppliers with suitable production processes were able to be identified and qualified. The internal production processes for the DampTronic® II shock absorber were also defined and implemented together with our colleagues from Process Development.
The comprehensive expertise of the shock absorber specialists impressed the Bavarian premium manufacturer. And not only that: As a semi-active suspension system that combines all the prerequisites for exceptionally comfortable and uncompromisingly safe driving at a reasonable cost, the system is currently being launched in series production by other car manufacturers.
The engineers at BILSTEIN were faced with a complex task: to develop a suspension system that not only meets BMW’s high standards, but also stands out in a highly competitive market. But the suspension experts succeeded in mastering the challenge.
Read story